[SUCCESS STORY NOVARES] FMEA challenges and solutions for OEMs: effective risk management and regulatory compliance
In an industrial context where product quality and conformity are more important than ever, original equipment manufacturers (OEMs) need to adopt rigorous methods and tools to guarantee the reliability of their products. Failure Mode, Effect and Criticality Analysis (FMEA) is one of the central methodologies for identifying and mitigating risks in manufacturing processes. However, the growing complexity of products and processes makes it essential to use specialized software to manage these analyses effectively. This interview explores the challenges and solutions associated with the adoption of dedicated FMEA software in the automotive industry, particularly in the production of plastic parts.
Jean-François Chocquet, Core Engineering Manager at Novares, highlights the requirements imposed by automakers for rigorous FMEA management via specialized tools, as well as the importance of data centralization and software fluidity in maintaining productivity and regulatory compliance. He explains the reasons for choosing Skill Software's solution as the tool for managing FMEAs, including the support received to ensure a successful transition to these new technological solutions, while guaranteeing regulatory compliance and smooth integration of the tool into existing processes.
Can you introduce yourself and the challenges you face in terms of FMEA?
"I'm Head of Core Engineering at Novares, a supplier of automotive parts to virtually every brand in the world. We produce mainly plastic parts, sometimes with metal components, and we're working hard to replace traditional metal parts with plastic alternatives. For example, we have replaced the metal cylinder head cover with a plastic version, incorporating additional functions such as pressure regulation and oil decanting. My department works across the board through our research centers in the USA, India, China, Turkey, Morocco and France. We are responsible for standardizing development methods from an engineering point of view."
FMEA is a systematic method used to identify and evaluate potential failures in a process or product, and to prioritize their criticality according to their effects on the system. OEMs (Original Equipment Manufacturers) in the production of plastic parts, particularly in the automotive sector, face several specific FMEA challenges:
- Material complexity: The transition from metal to plastic parts introduces complexity in terms of material properties. Plastics have different mechanical, thermal and chemical behaviors, requiring in-depth analysis to anticipate failure modes.- Multifunctional integration: Plastic parts, often designed to integrate several functions, increase the number of potential failure modes. For example, a plastic cylinder head cover integrating pressure regulation and oil decanting functions needs to be analyzed for possible failures related to each integrated function.
- Quality control and production variability: The production of plastic parts is subject to variations in the injection molding process, such as variations in temperature and pressure, which can affect quality and lead to defects. The FMEA must identify the critical parameters of the manufacturing process and assess their impact on final product quality.
- International standards and regulations: Operating on an international scale, OEMs must comply with various standards and regulations in different countries (such as IATF 16949 for the automotive industry). Each market may have specific safety and performance requirements, increasing the complexity of FMEA analysis.
- Cross-functional collaboration: development teams are often spread across the globe, as in the case of Novares, with research centers on different continents. Standardization of engineering methods and effective communication between these teams are fundamental to a coherent and exhaustive FMEA analysis.
- Innovation and continuous development: Ongoing innovation to replace traditional metal parts with plastic alternatives requires regular updating of FMEA analyses to incorporate new materials and technologies. This includes assessing the risks associated with the introduction of new manufacturing processes or new plastic formulations.
- Durability and recyclability: Environmental issues and product sustainability are putting additional pressure on OEMs to ensure that plastic parts not only perform well, but are also recyclable. FMEA must include analyses of the environmental impact and recyclability of the materials used.
FMEA is therefore an essential tool for OEMs in the production of plastic parts, enabling them to proactively identify potential risks, implement preventive and corrective measures, and guarantee optimum quality and safety of end products.
What were the initial motivations behind the choice of Skill Software as the FMEA software publisher?
"Before adopting Skill FMEA Pro, we were using Excel files to manage our product and process FMEAs, as well as our control plans. This involved a lot of copy-and-pasting between files, which increased the risk of errors and inconsistencies, especially with FMEAs that could exceed 2000 lines. During audits, we were often confronted with inconsistencies between the special characteristics defined in the product and those found in the control plan or process. We therefore looked for a software package capable of resolving these problems of continuity and accuracy. After examining several options, Skill FMEA Pro stood out."
Data centralization is one of the key issues addressed by a FMEA tool, as it allows all product, process and control plan FMEA information to be consolidated in a single database. This eliminates the scattering of data over several files and reduces the risk of lost or duplicated information, while facilitating access to data for all team members, regardless of their geographical location.
Dedicated software also helps reduce errors and inconsistencies. Manual copy-and-paste between different Excel files, a major source of errors, is replaced by automated data transfer. Dynamic links between the different parts of the FMEA (product, process, control plans) ensure that any modification is automatically updated in all the documents concerned, guaranteeing perfect consistency.
Regulatory compliance and auditability are also greatly enhanced by the use of FMEA software. During quality audits, it is essential to prove compliance with standards such as IATF 16949. The traceability and change history features offered by such software ensure total transparency, facilitating audits and confirming that the special features defined in the product are consistent with those in the control plan and process.
In terms of efficiency and time savings, dedicated software automates many of the repetitive tasks involved in FMEA management. This reduces the time spent checking and correcting errors, enabling teams to concentrate on continuous process and product improvement. Collaboration is also improved, especially for internationally dispersed development teams.
Finally, dedicated software offers advanced analysis and reporting capabilities, enabling the generation of detailed, customized reports. These reports are essential for identifying trends, high-risk areas and opportunities for improvement. Access to accurate, real-time data enhances decision-making and proactive risk management.
Can you tell us about the benefits and results you've seen from using Skill FMEA Pro ?
"Currently, we're still in the development and deployment phase. Since July, all new projects have been required to use this software. This process has been accelerated by the demands of certain customers such as Ford and GM, who require us to use a specialized solution to manage FMEAs more rigorously, compared with Excel files. That's why we've gone from a simple desire for improvement to an absolute necessity, because without this type of software, customers refuse to award their projects.
Skill's strength is their availability and flexibility. They're always ready to listen and find solutions. They're not locked into a commercial context where, as soon as things get a little out of hand, they don't do it or will charge us again. They really don't think that way. What I like about them is that as long as they don't think we can use the software, they continue to support us. That's really good. Every time I call them, there's always someone who answers right away, and I always get an answer within an hour at the most. It's really appreciated."
The pressure exerted by automotive manufacturers on OEMs to adopt dedicated FMEA solutions is growing. This requirement is driven by the need to ensure better traceability, error reduction and strict compliance with quality and safety standards. Automakers are imposing these requirements for several reasons. Firstly, expectations of part quality and performance are increasingly high, requiring thorough and accurate analysis of potential failure modes. Secondly, the growing complexity of modern vehicles, with ever greater integration of electronic systems and new technologies, makes it essential to use sophisticated solutions to manage the risks associated with these innovations.
Faced with this pressure, OEMs need to accelerate the transition to the adoption of dedicated FMEA tools. Specialized software can not only meet OEM requirements, but also boost operational efficiency. By centralizing data and automating many tasks, these tools reduce the risk of errors and improve the consistency of information. This translates into better project management and increased ability to meet deadlines and customer specifications.
The support provided by a dedicated FMEA solution vendor is also crucial to the success of this transition. OEMs benefit from technical and functional support to maximize the use of the tool. The editor must provide ongoing assistance, tailored training and availability to answer questions quickly and resolve any problems. This support ensures that users feel confident and competent in using the software, which is essential for successful integration.
The editor must also demonstrate flexibility and adaptability. Every OEM has specific needs and unique processes. A good vendor must be able to adapt its offering and services to meet these particularities, without imposing additional costs for every minor adjustment. This flexible, customer-focused approach builds OEM confidence and satisfaction, helping them to get the most out of their investment in FMEA software.
Which elements of the Skill FMEA Pro solution and Skill Software support do you find most beneficial?
"The software's responsiveness is impressive. Even on a Citrix system, known for its latency, Skill FMEA Pro offers fast response times, as if the software were installed directly on the PC. The interface is simple and ergonomic, despite the complexity of the subject. Many competing solutions have heavy, complex interfaces with numerous sub-menus, but Skill FMEA Pro remains accessible and intuitive."
The importance of software dedicated to FMEA management lies partly in its speed and fluidity of use, even on slow operating systems. This operating capability is essential, as such software has to manage large databases containing thousands of lines of technical information, process parameters and control plans. If the software is slow or unresponsive, it can considerably slow down daily operations and reduce productivity. Fast, fluid FMEA software must therefore offer fast response times even on less powerful IT infrastructures. This requires extensive code optimization and efficient management of system resources to minimize latency.
Equally fundamental is the software's ability to handle large amounts of data without sacrificing performance. This calls for robust database architecture and efficient data processing algorithms. Data management must be optimized to enable fast searches, instant updates and fluid handling of information, even when several thousand lines of FMEA data are involved.
Software reliability and stability also play key roles in ongoing operations. Software that crashes frequently or is prone to bugs can lead to data loss and service interruptions, negatively impacting production and product quality. Consequently, FMEA software must be rigorously tested and regularly updated to guarantee optimum performance and a stable user experience.
Finally, the software's ergonomics and user-friendliness directly influence user acceptance. A simple, ergonomic interface enables users to navigate easily between different functions and modules, reducing the time needed to perform complex tasks. Intuitive software also reduces the need for intensive training and enables faster adoption by teams. This is particularly important in a production environment where time is a precious resource.
In a few words, how would you describe Skill Software and their Skill FMEA Pro solution?
"The availability and responsiveness of their team are remarkable. Their software is reliable and ergonomic. Even if certain functions could be improved, we have never encountered a crash. The reliability and ergonomics of the solution are the strong points."
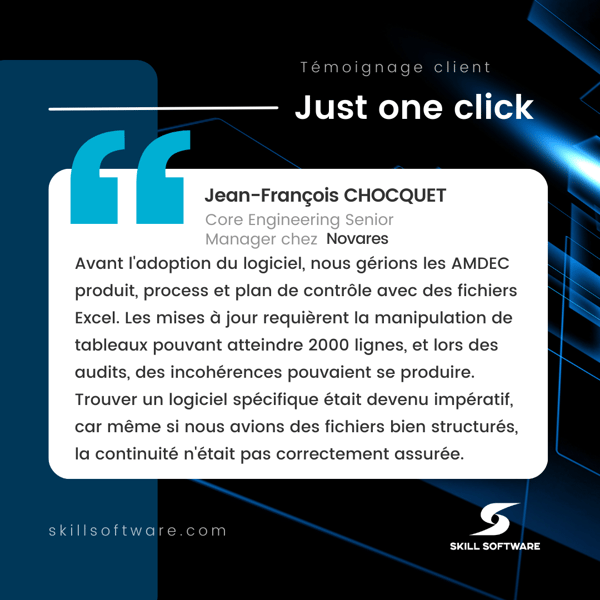